A catastrophic failure of a thermal wet oxidation process can occur if the safety interlocks for a no-flow condition are disabled, allowing the system to operate without slurry flow and continue to feed hot air. This condition can ignite organic solids in the heat exchangers and cause a fire and explosion.
Treatment processes often contain controls that monitor for unsafe conditions and prevent equipment from operating or will initiate a shut down sequence before property damage or injury to nearby staff can occur.
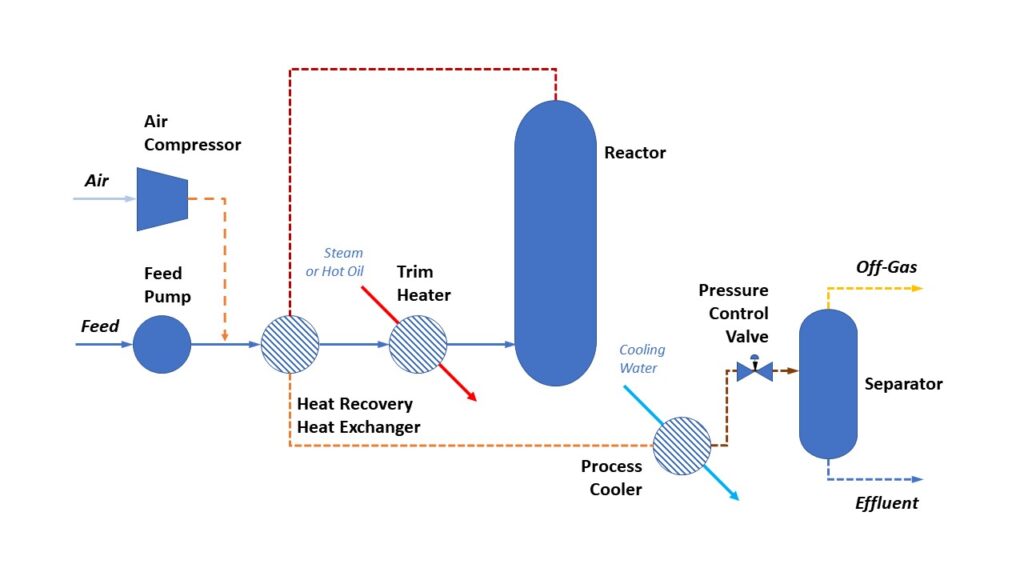
The typical wet oxidation system (Figure 1) is a continuous process using rotary compressor and pump to compress the air (or oxygen) to the required operating pressure. The feed stream is introduced using two-chamber high pressure hydraulic-oil pumps with check valves and cylindrical sleeves. Double-pipe heat exchangers serve to recover energy from the reactor effluent and use it to preheat the feed/air mixture entering the reactor. Auxiliary energy, usually steam, is necessary for startup and can provide trim heat if required. The residence time in the reactor vessel is several hours at a temperature that enables the oxidation reactions to proceed. In some applications this can be total mineralization. The reactor is a bubble column; it is coupled after the heat exchanger with a separator for the separation of the effluent and the off-gases. Since the oxidation reactions are exothermic, sufficient energy may be released in the reactor to allow the wet oxidation system to operate without any additional heat input at or above COD > ~10,000 mg/L.
A facility received sanitary wastewater and a combined industrial waste from magnetic data memory medial production, a commercial hazardous waste treatment facility, and a pesticide and herbicide manufacturing facility. The corrosivity of the combined wastewater required that the wet air oxidation system used titanium piping and a titanium clad reactor vessel. Toxicity of the wastewater required combined biological and powdered activated carbon treatment (PACT). The excess collected sludges consisting of magnetic iron and chrome oxides, biosolids, and spent powdered activated carbon with adsorbed toxic compounds. Pilot testing had previously determined that operation at 450 degrees Fahrenheit and 700 psi detoxified materials or rendered them insoluble for removal.
Once running continuously, the organic material in the stream combines with 700 psi air and produces an exothermic reaction. This is possible because the partial pressure of oxygen is 147 psig (by contrast, the partial pressure of oxygen is 3.0 psi in our atmosphere at sea level) and the process recovers the heat in the effluent through heat exchange with the influent.
System startup requires on the feed pumps to a minimum pressure and flow, the external heaters, and then the air compressor online. Once the system begins generating heat, the external heaters automatically taper their heat input. Inexperienced operators will find that if the pressure or flow drops below the minimum level for a period of 10 seconds the system will shut off the air compressor and heater and bring the system offline.
At some point, the pressure safety interlocks were bypassed and the timer delay for flow was extended significantly. The feed pumps hydraulic sleeves failed, creating a no flow situation. Though the hydraulic oil system lost pressure, the check valves continued to flow from one chamber to the other sending a pressure “pulse” that reset the shut-off timer. The air compressors continued to feed compressed dry air through the feed line, drying the solids in the line. The heater continued to heat the solids in the presence of pressurized air. The solids ignited. The burning solids raised the pipe temperature above the softening point of titanium. The high pressure and temperature caused the pipe to bulge and burst. The titanium pipe ignited and suddenly 40 feet of titanium pipe vaporized into a fine white powder. The burning metal reached the reactor vessel and vaporized the contents. The steam and solids escaped the reactor in a sudden release. The high pressure steam melted all the plastics and rubber in its path including the tires, shield, seating and dash of a nearby Cushman shuttle. No one was injured.
In working with the insurer to determine the cause and magnitude of the loss, we found that both pressure and flow safety interlocks were compromised. This event demonstrated the high cost associated with multiple, simultaneous failures and the value of a detailed node by node what if analysis that is part of any process safety management program.